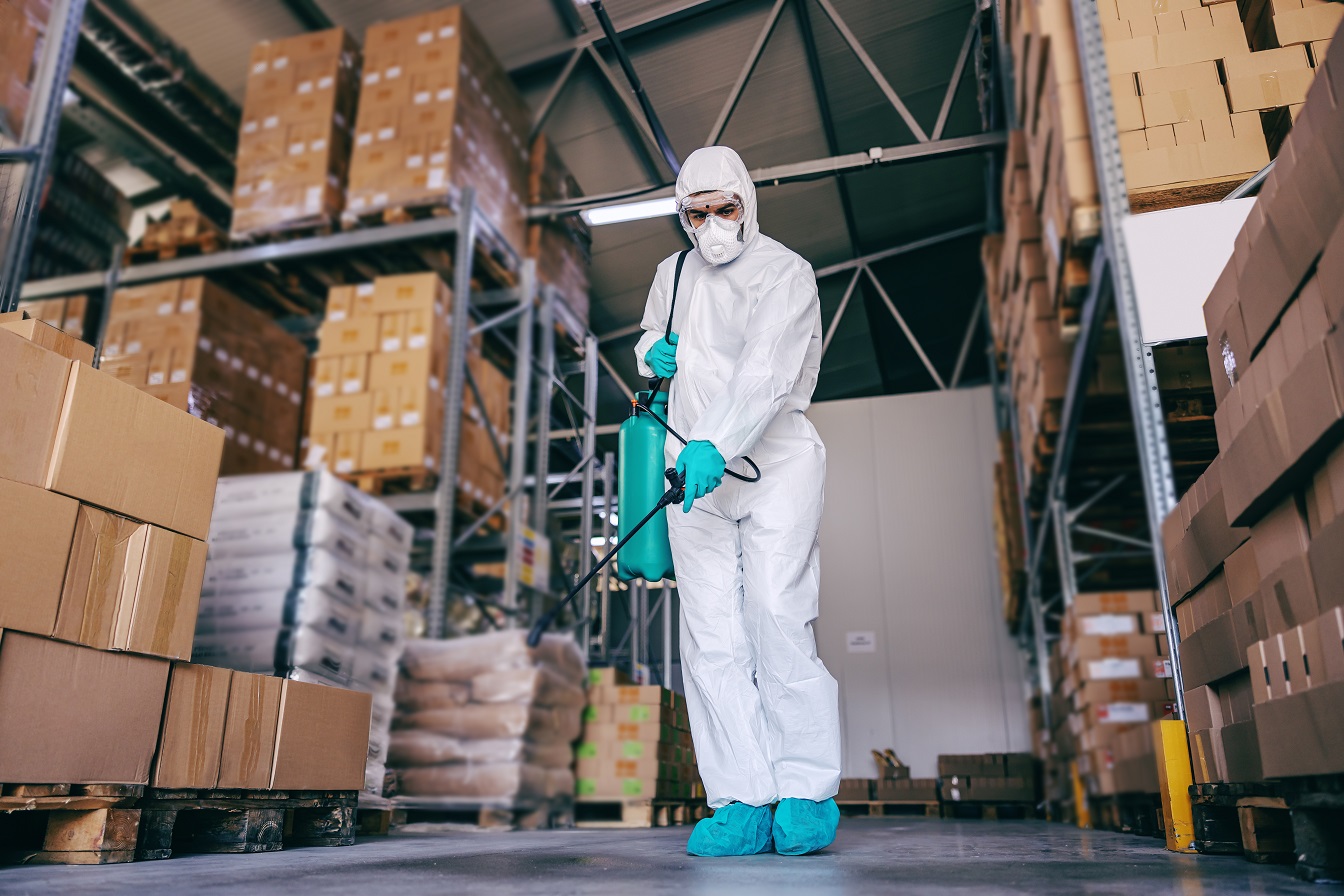
By Darlene Bernd, Content Marketing Manager
Anago Cleaning Systems
A well-organized, clean, and disinfected warehouse isn’t just about appearances – it directly impacts inventory protection, employee safety, and overall cost savings. A well-maintained facility reduces product damage, extends equipment lifespan, and minimizes health risks.
From preventing damage and contamination to improving efficiency and safety, a well-maintained warehouse can make a huge difference. Here’s how you can achieve it and why it matters.
Risks of a Dirty and Disorganized Warehouse
Increased Risk of Product Damage
- Dust, dirt, and clutter can compromise product quality and lead to costly damages. When dust accumulates on inventory, it can affect the appearance and even the functionality of products, especially in industries like food, electronics, and pharmaceuticals.
- Spills and leaks can ruin packaging and create unsafe storage conditions. A small spill might seem harmless, but liquid damage can weaken boxes, cause labels to loosen, and even lead to mold growth.
- Pests thrive in unclean areas. Crumbs, spills, and cardboard debris create the perfect environment for rodents and insects. Pests can chew through packaging, contaminate products, and cause major compliance issues – especially in food and medical storage facilities.
Health and Safety Hazards
- Slips, trips, and falls are more common in cluttered spaces, making it essential to keep walkways clear and organized.
- Poor air quality from dust and mold can cause respiratory issues, leading to discomfort, decreased productivity, and even long-term health concerns. Regular cleaning, proper ventilation, and routine air quality checks help create a healthier and safer work environment.
- Regular cleaning of warehouses plays a crucial role in minimizing fire hazards. Warehouses often store flammable materials such as chemicals, fuels, or paper products, so dust, debris, and improper storage can lead to an increased risk of fire.
Inefficient Operations and Higher Costs
- Time spent searching for misplaced items lowers productivity, leading to delays in completing tasks and increased frustration among team members. Wasted time impacts the efficiency of daily operations.
- Damaged inventory leads to financial losses and supply chain disruptions, as improperly stored items are more prone to wear and tear. Replacing damaged goods results in higher operational costs and disruptions in the supply chain.
- Neglecting routine cleaning and upkeep leads to the deterioration of equipment, shelving, and flooring over time. Dust, debris, and other substances can cause wear and tear on machinery, forcing more frequent repairs or replacements.
How Cleanliness Protects Your Inventory and Building
Prevents Product Contamination
- Regular disinfection removes bacteria, mold, and allergens that can damage goods. Consistently eliminating harmful microorganisms creates a more hygienic environment, contributing to the longevity of your products.
- Proper ventilation reduces moisture buildup that can cause mold growth. Creating a dry and controlled environment is essential for preserving your inventory and the overall structural integrity of your warehouse.
- Storing hazardous materials in designated secure areas prevents accidental spills and protects inventory.
Extends the Lifespan of the Warehouse Facility
- Dirt and grime accelerate surface deterioration, leading to cracks, stains, and potential structural damage. Routine floor cleaning prevents damage like corrosion of concrete and wood surfaces.
- Regular HVAC maintenance keeps air quality high and prevents damage by ensuring that air filters, ducts, and vents are clean and functioning. Regulated airflow, temperature, and humidity levels protect your inventory from fluctuations, moisture, and airborne contaminants.
- Organized storage prevents overloading of shelves, reducing structural strain by properly distributing and storing items according to weight limits and safety guidelines. Maintaining an orderly layout minimizes the risk of overburdening shelves and racking systems.
Steps to Maintain a Clean and Organized Warehouse
Implement a Regular Cleaning Schedule
- Assign daily, weekly, and monthly cleaning tasks to ensure consistency and a high standard of cleanliness throughout the warehouse. Daily tasks involve sweeping, emptying trash, and sanitizing high-touch surfaces to prevent debris buildup.
- Schedule deep cleaning jobs for floors, shelving, and ventilation systems to remove accumulated dust, debris, and contaminants that regular cleaning may miss. Deep cleaning floors helps eliminate grime, grease, and potential slip hazards, ensuring a safer work environment for employees and prolonging the lifespan of warehouse surfaces.
Invest in Professional Commercial Cleaning Services
- As warehouses present distinctive cleaning requirements, their specific needs set them apart from other commercial properties, such as:
* Epoxy coatings and polished concrete floor maintenance
* Chemical and other spill cleanup
* Duct and vent cleaning
* Disinfection and green cleaning solutions - Professional cleaning technicians know how to tackle any warehouse hazard, keeping your space OSHA-compliant and your team safe.
A well-organized, clean, and disinfected warehouse is crucial for protecting your inventory, prolonging product life, and cutting operational costs. Optimizing storage solutions, implementing regular cleaning routines, or hiring professional commercial cleaning services creates a safer, more efficient, and cost-effective warehouse environment.
Start today and see the benefits firsthand!